완제 공정 중 니트로사민 발생 기전
고형 경구제 제조 단위공정과 공정별 개요
고형 경구제(정제, 캡슐 등) 제조는 여러 단위공정으로 구성되며, 각 공정은 니트로사민 생성에 영향을 미칠 수 있습니다.
건식과립(Dry Granulation): 압축 또는 롤러 컴팩션을 통해 분말을 직접 과립화하는 공정으로, 수분을 사용하지 않아 습식과립 대비 니트로사민 생성 위험이 낮습니다.
습식과립(Wet Granulation): 결합제 용액을 분말에 첨가해 과립을 형성하는 공정으로, 수분과 열이 존재해 아민과 아질산염의 반응이 촉진될 수 있습니다.
건조(Drying): 과립화 후 수분을 제거하는 단계로, 40~80°C의 온도에서 진행되며, 고온·고습 환경이 니트로사민 생성에 영향을 줄 수 있습니다.
정립(Milling/Sieving): 과립의 입자 크기를 균일하게 맞추는 과정으로, 물리적 변화가 주를 이루나, 분쇄 시 열 발생이 있을 수 있습니다.
혼합(Blending): API와 부형제, 기타 첨가제를 균일하게 혼합하는 단계로, 고체상에서의 미세 반응이 일어날 수 있습니다.
활택(Lubrication): 활택제(윤활제)를 첨가해 타정 시 마찰을 줄이는 공정으로, 마그네슘스테아레이트 등 금속염이 사용됩니다.
타정(Compression): 혼합된 분말 또는 과립을 압축해 정제를 만드는 단계로, 고압·마찰에 의한 온도 상승이 일어날 수 있습니다.
코팅(Coating): 정제 표면에 폴리머, 색소, 가소제 등을 입혀 방출조절, 안정성, 외관 개선을 도모하는 공정으로, 유기용매 및 열이 사용될 수 있습니다.
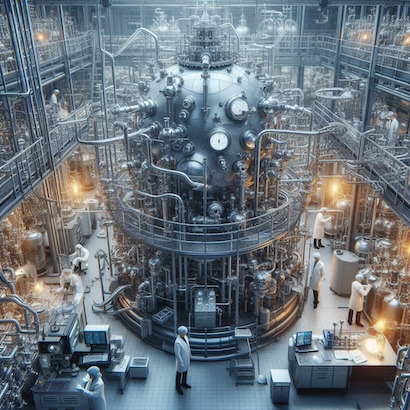
단위공정별 사용 첨가제와 기능별 분류
각 공정에서 사용되는 첨가제는 기능별로 다음과 같이 분류됩니다.
부형제(Diluent): 미세결정셀룰로오스(MCC), 락토스 일수화물, 만니톨, 이인산칼슘, 수크로스
결합제(Binder): 포비돈(Povidone, PVP), 하이드록시프로필셀룰로오스(HPC), 하이드록시프로필메틸셀룰로오스(HPMC), 젤라틴, 전분
붕해제(Disintegrant): 나트륨전분글리콜레이트(SSG), 크로스카르멜로스나트륨, 크로스포비돈, 카르복시메틸셀룰로오스칼슘, 옥수수전분
활택제(Lubricant): 마그네슘스테아레이트, 칼슘스테아레이트, 스테아르산, 탈크, 폴리에틸렌글리콜(PEG)
방출조절폴리머(Release-Controlling Polymer): 에틸셀룰로오스, 유드라짓(Eudragit RL/RS), HPMC, 폴리아크릴산, 카보폴
코팅제(Coating Agent): HPMC, 폴리비닐알코올(PVA), 셸락, 유드라짓, 이산화티타늄, 활석
첨가제별 2차/3차 아민 및 니트로소화제 포함 가능성
부형제: MCC, 락토스, 만니톨 등은 천연 유래로, 제조·정제 과정에서 미량의 아질산염(nitrite) 불순물을 포함할 수 있습니다. 락토스의 경우, 최신 분석법으로도 0.01~0.5ppm 수준의 nitrite가 검출될 수 있습니다.
결합제: PVP, HPC 등은 피롤리딘 구조를 포함하며, 가수분해 시 2차 아민(피롤리딘) 생성 가능성이 있습니다. 일부 PVP, 크로스포비돈은 nitrite 함량이 0.5~11ppm까지 보고된 바 있습니다.
붕해제: SSG, 크로스카르멜로스나트륨, 크로스포비돈 등은 제조공정 중 nitrite 불순물이 혼입될 수 있으며, 크로스포비돈은 2차 아민 구조를 포함합니다.
활택제: 마그네슘스테아레이트, 칼슘스테아레이트 등은 자체적으로 아민을 포함하지 않으나, 제조공정 중 오염 가능성이 있습니다. 탈크는 광물성으로, 질소 함유 불순물은 드물지만, 일부 등급에서 미량 검출 사례가 있습니다.
방출조절폴리머: 유드라짓 RL/RS는 4급 암모늄기(10%/5%)를 포함하며, 분해 시 3차 아민(예: 트리에틸아민, 디이소프로필에틸아민) 생성 가능성이 있습니다.
코팅제: HPMC, PVA 등은 아민 구조를 포함하지 않으나, 유드라짓 계열은 위와 같이 3차 아민 전구체가 될 수 있습니다.
니트로소화제(아질산염, nitrite)는 주로 부형제, 결합제, 붕해제 등 천연 유래 첨가제에서 미량 존재할 수 있으며, 제조공정 중 용수, 공정기기, 포장재 등에서 추가로 유입될 수 있습니다.
니트로사민 생성 가능성이 높은 공정과 촉진 조건
니트로사민 생성 가능성이 가장 높은 공정은 습식과립, 건조, 코팅 공정입니다.
습식과립: 수분, 열(40~80°C), 산성 pH가 동시에 존재해 아민과 아질산염의 반응이 촉진됩니다. 과립화 과정에서 부형제·결합제 내 아민류와 nitrite가 접촉하며, 고체상 반응이 일어날 수 있습니다.
건조: 고온(60~120°C)에서 수분이 증발하며, 잔류 nitrite와 아민류가 농축되어 반응성이 증가합니다.
코팅: 유기용매, 고온(40~60°C), pH 변화 등으로 인해 코팅제 내 3차 아민(유드라짓 등)과 nitrite가 반응할 수 있습니다. 특히 유드라짓 RL/RS는 4급 암모늄기가 분해되어 3차 아민을 방출할 수 있습니다.
이러한 공정에서는 온도 상승, 수분 존재, 산성 환경, 장시간 반응 등이 니트로사민 형성을 촉진하는 주요 요인입니다. 습식과립과 건조 공정은 부형제·결합제 내 아민과 nitrite가 직접 접촉하는 환경을 제공하며, 코팅 공정은 고온·유기용매 조건에서 3차 아민의 분해와 니트로소화 반응이 가속화됩니다.
결론적으로, 완제의약품 제조공정에서 니트로사민 생성은 첨가제 내 2차/3차 아민과 nitrite의 동시 존재, 그리고 습식과립·건조·코팅 등 고온·고습·산성 조건에서 가장 위험성이 높습니다. 첨가제의 nitrite 함량 관리, 공정조건 최적화, 원료·공정별 위험평가가 필수적입니다
참고문헌
Meggle Pharma, RISK MITIGATION OF NITROSAMINES FORMATION IN DRUG PRODUCTS:
BASF, Control nitrosamines with low nitrite excipients from BASF